Technology: Straw Heating

Straw and Agricultural Residues for District Heating
Straw and corn stalks is the cheapest fuel for boilers and CHP in Ukraine and in many other countries. In countries with large production of grain, it is also abundant. It is, however, also one of the more difficult fuels with higher ash content than wood, normally in the range of 2-10%, and a low ash melting point, 680-900 °C (at 680 °C the ash get sticky and start to form slags, at 900 °C it is a thick liquid). Straw is widely used for district heating in Denmark, where 9% (12 PJ) of district heating comes from straw firing and a small additional contribution is from straw used in biogas plants.
Straw can be used in CHP plants and in heat only boilers, from smaller domestic boilers to large-scale CHP plants. The CHP technology is normally steam turbines for larger plants and organic ranking cycle turbines for plants up to around 20 MW heat output. For installations above 1 MW, the plants are usually equipped with flue gas condensation and the they can reach combined efficiencies above 100% (with lower heating value - LHV* - as reference). The main technologies are:
- Boilers for small bales with automatic or manual firing, for farms etc. typical heating capacities 40-100 kW.
- Boilers for large bales that are batch-fired (the bale is carried with a tractor into the boiler chamber), typical heating capacities 100-500 kW, used for institutions etc.
- Boilers with automatic firing of large bales with moving grates, typical heating capacities 1-25 MW.
- CHP with automatic firing of large bales, using moving grates typical heating capacities 10-150 MW. Electric efficiencies range from around 15% for the smallest to 30% for mid-range (60-100 MW heating).
- CHP with automatic firing of large bales, using fluidised bed combustion, typical heating capacities 20-300 MW.
* For lower heating value (LHV) the energy in the fuel does not include the condensation of the vapour in the flue gas, and if the vapour is condensend it is possible to reach above 100%. For higher heating value (HHV), energy of condensation of vapour in the flue gas is included.
An important issue for straw use is the supply. Plants typically have long-term contracts with farmers or they are placed on farms that produce straw. The contracts should specify size and type of straw bales, and also water content. Some plants are made to fire both straw and other biomass, as wood chips to avoid dependence on too few fuel suppliers.
Another issue is the storage of straw, as this must be stored from harvest for the entire heating season until next harvest. Often this is done with a combination of a storage next to the plant with straw for at least 2 days full capacity combined with storages at farms or on fields, where the straw is covered by plastic to avoid too much humidity.
The main air emissions are particles and NOx. SO2 emissions are low due to low sulphur content in straw. Due to high ash content and resulting dust in flue gas, the flue gas is normally filtered to collect fly ash. The filters are relatively expensive for small installations, so most installations are at least a few hundred kW Bag filters or electrostatic filters can ensure low particle emissions. For larger installations, also NOx cleaning is often required in EU countries.
Most of the ash is bottom ash while a smaller part is fly ash. The ash can normally be used on fields as it contains kalium that is a plant nutrient. When grain is harvested, most kalium (2/3) is in the straw, and to maintain kalium in the soil, the ash can be returned to the field. Only a small part of the harvested phosphor and nitrogen is in the straw, less than 20%, with the remaining +80% in the grain.
There is a small content of heavy metals in the ash, normally the content in the bottom ash is negligible while the amount in the fly ash can be higher.
Examples
Mørke District Heating
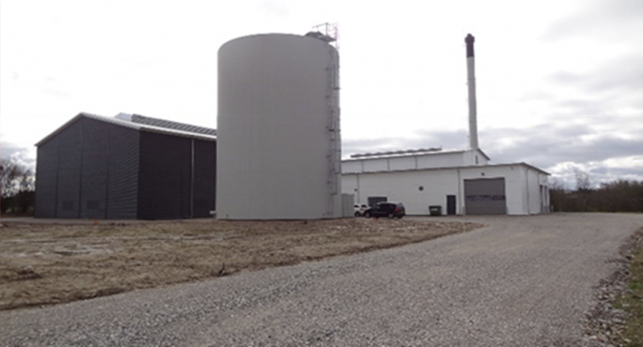
In the Danish town Mørke with 1698 inhabitants, the local district heating company with 609 connected consumers opened in 2018 in a straw-fired boiler of 4,5 MW combined with a storage for large straw bales with automatic firing and a heat storage in the form of a 1400 m3 hot water tank with a heat storage capacity of 80 MWh.
Lisbjerg/Aarhus Straw Fired CHP Plant
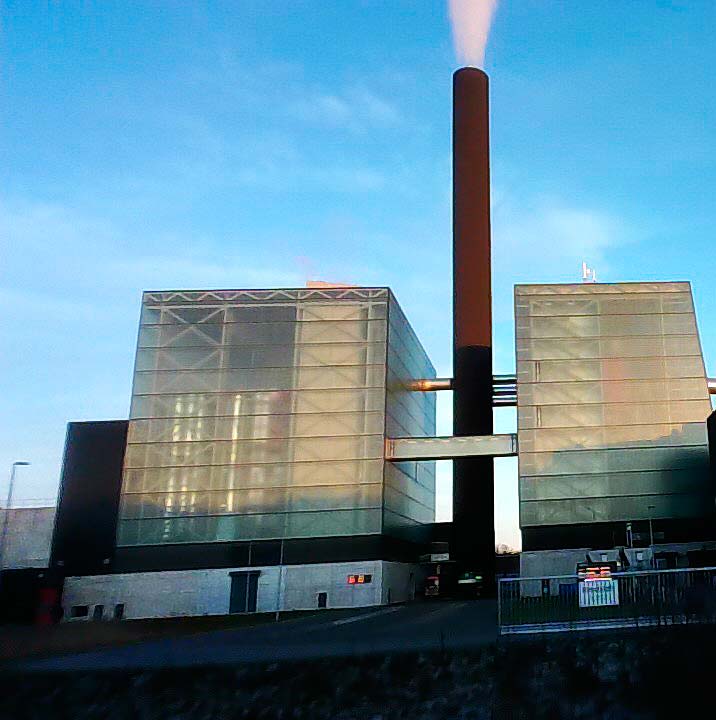
The district heating company of the Danish town Aarhus with 285.000 inhabitants opened in 2017 a straw fired CHP plant in the suburb Lisbjerg with 37 MW electric capacity and 77 MW heating capacity. The plant has a straw storage for 3 days operation with full capacity. The plant is equipped with a bag filter, NOx-cleaning and condensation of the flue gas. The flue gas condensation enables an efficiency of heat and electricity together of 100%. The plant can operate of straw alone and with a combination of 50-100% straw and 0-50% wood chips.

Technical parameters for straw-fired heat only boilers
- Sizes: from 50 kW to 25 MW. They can also be larger.
- Efficiency: for boilers above 1 MW with flue gas condensation, 100-104%, based on lower heating value (LHV).
- Lifetime: Technical lifetime 25 years.
- Space requirements: 200 m2/MW, larger if large straw storage is onsite.
- Forced outage: 4% of time.
- Emissions:
- NOx: 70-90 g/GJ fuel (without NOx cleaning).
- Particles: without cleaning 200-300 mg/Nm3 flue gas, with bag filters it is possible to reduce to 0,3 g/GJ. With bag filters it is easy to meet EU requirements of 45 and 30 mg/Nm3 that are required for boilers of respectively 1-5 MW and above 5 MW according to EU Medium Combustion Plant Directive (MCP).
- Smaller plants will also have emissions of CO and OGC from incomplete combustion.
Financial parameters for straw-fired heat only boilers 3-10 MW
- Nominal investment: 900.000 €/MW heat output.
- Fixed O&M: 52.000 MW €/MW heat output.
- Variable O&M: 0.67 €/MW heat output + electricity use of 22 kWh/MWh heat output, including automatic firing system.
Technical parameters for straw-fired combined heat and power (CHP) plants
- Sizes: from 10 MW to 300 MW heating capacity.
- Efficiencies based on lower heating value:
- Electric efficiency 15% for smaller CHP (15 MW heating, organic ranking cycle turbine - ORC), 30% for larger CHP (50 MW heating and larger, steam turbine).
- Total efficiency 100% with flue gas condensation.
- Lifetime: Technical lifetime 25 years.
- Space requirements: 1000 m2/MW, larger if large straw storage is onsite.
- Forced outage: 3-4% of the time.
-
Emissions:
- NOx: 70-90 g/GJ fuel (without NOx cleaning).
- Particles: With bag filters it is possible to reduce to 0,3 g/GJ, which can meet EU requirements of 30 mg/Nm3 that are required for boilers of 5-50 MW fuel according to EU Medium Combustion Plant Directive (MCP).
Financial parameters for straw-fired CHP with 15 MW heat output, ORC turbine**
- Nominal investment: 1.200.000 €/MW heat output equal to 6.900.000 €/MW electric output.
- Fixed O&M: 54.000 MW €/MW heat output equal to 318.000 MW electric output.
- Variable O&M: 0.7 €/MW heat output equal to 4,5 €/MWh electric output
Financial parameters for straw-fired CHP with 100 MW heat output, steam turbine**
- Nominal investment: 1.500.000 €/MW heat output equal to 3.500.000 €/MW electric output.
- Fixed O&M: 54.000 MW €/MW heat output equal to 126.000 MW electric output.
- Variable O&M: 0.9 €/MW heat output equal to 2,1 €/MWh electric output.
** The financial parameters are per MW heat output or per MW electric output. For cost estimates, choose one of the output parameters and multiply with the financial parameters.
Sources for information
Calculation of energy and economy
Cases
- Mørke District Heating: moerkefjernvarme.dk
Aarhus / Lisbjerg Straw Fired CHP plant
Technology suppliers and installers
- linkaenergy.com
- faust.dk (boilers below 1,5 MW)
Technical advice
Other sources
- Ash melting temperature: Characterization of Ash Melting of Reed and Wheat Straw Blend, Siim Link, Patrik Yrjas (Åbo Akademi University), Daniel Lindberg and others - researchgate.net
- Content of plant nutrients in ash from straw firing: Separation og genanvendelse af aske fra biobrændselsanlæg, chapter 8: Anvendelse af halmaske til landbrugsformål. Danish Environmental Agency 2004 - www2.mst.dk
- Particle emissions from straw combustion: Halmfyr, Miljøprojekt 1958, Danish Environmental Agency, 2017 - mst.dk